变速箱系统作为拖拉机上技术密集程度最高的一个部分,在拖拉机技术发展过程中一直都是核心C位的存在,尤其是在200马力以上的高端大马力拖拉机领域更是如此,近年来国内拖拉机的新能源趋势越发的明显,尤其是混合动力拖拉机,在国内市场掀起了滔天巨浪,今天我们就分享一下关于混合动力拖拉机的传动系统相关信息。
混合动力拖拉机结合了传统内燃机和电动机的双重动力源,其变速箱系统是实现动力高效传递与分配的核心部件。相比传统拖拉机,混合动力变速箱需协调发动机与电机的协同工作,优化能量利用效率,同时满足农业机械对高扭矩、低排放和灵活操控的需求。以下是混合动力拖拉机变速箱系统的关键要点:
一、系统组成与功能
动力输入模块
内燃机(ICE):提供持续动力,适合中高速稳定工况。
电动机(EM):支持瞬时高扭矩输出(如起步、爬坡)和能量回收(再生制动)。
动力耦合装置:通过行星齿轮、离合器或专用耦合器整合两动力源,实现并联、串联或混联模式。
变速机构
多挡位变速器(如AMT、PST):适应不同作业场景(耕作、运输等)的扭矩需求。
无级变速器(CVT):实现平滑调速,提升能效,但需兼顾高扭矩承载能力。
能量管理系统
电池组(PHEV/HEV):存储电能,支持纯电模式运行(如温室作业)。
控制单元(ECU):实时优化动力分配策略,平衡发动机效率区与电机辅助需求。
辅助系统
冷却系统:防止电机和电池过热。
传感器网络:监测转速、扭矩、温度等参数,确保系统稳定。
二、混合动力变速箱类型
并联式混合动力
发动机与电机通过机械耦合共同驱动车轮,结构简单,适合高负荷作业。其典型应用为约翰迪尔于2019年汉诺威农机展上推出的eAutopower系列变速箱系统,其结构为将原来HMCVT变速箱内动力分流液压传动支路改为电机驱动,也就说将原来HMCVT变速箱内部的静压传动单位更换为电力驱动,并通过行星机构实现和机械传递部分的动力合流,通过无极调整电驱部分的速度,最终实现整个变速箱系统的无极传动,也就是所谓ECVT变速箱。
优势:可直接机械传动,能量损失小;挑战:需复杂控制策略避免动力冲突。
缺点:对应机械传递部分的加工制造要求高,尤其是动力换挡部分的湿式多片、多组离合器控制加工等方面要求较高,制造成本也较高。
串联式混合动力
发动机仅驱动发电机为电池充电,电机独立驱动车轮。目前在市场上的典型应用为玉柴集团的IE-Power系列EVT变速箱,目前在国内众多二线主机厂都在选用这种方式的混合动力传动系统。其结构简单概述为一个柴油发动机+发电机+电机+一个2档的AMT变速箱。其结构要比并联式动力分流的混动变速箱简单很多
优势:发动机始终工作在高效区间;结构简单,制造成本及控制难度相比并联式混合动力变速箱要低很多;适用场景:频繁启停的轻载作业。
从另外一个侧面来说当下的混合动力拖拉机传动系统有插电式和增程式两种方式,国外主流和国内的一线大厂或者专业变速箱系统供应商一般都采用插电式混动,诸如约翰迪尔、采埃孚、中联重科、法士特等国内外头部企业都采用插电式混合动力变速箱;增程式国内主要是以玉柴的IE-Power系列变速箱。
三、技术优势
能效提升
发动机避开低效工况,电机填补扭矩缺口,混合动力拖拉机传动系的控制系统能将发动机和电机综合效率提升到最佳状态,结合当下的AI技术,能最大限度的降低车辆油耗,目前情况下综合油耗降低20%-40%。
再生制动回收能量,延长纯电作业时间。
环保与静音
减少尾气排放,纯电模式适用于封闭环境(如温室、养殖场)。
电机驱动显著降低噪音。
动态性能优化
电机瞬时响应提升牵引力,应对泥泞、坡道等复杂地形。
四、挑战与解决方案
高扭矩需求
采用高功率密度永磁电机,结合多挡变速器放大扭矩。
系统复杂度
模块化设计降低维护难度,AI算法优化控制策略(如模型预测控制)。
成本与可靠性
规模化生产降低电池与电机成本;强化密封设计适应粉尘、潮湿环境。
五、应用场景
纯电模式:短途轻载运输、精细化播种/施肥。
混合模式:犁耕、收割等高负荷作业。
智能扩展:与自动驾驶系统协同,实现精准农业。
六、未来趋势
电驱动桥集成化:将电机、减速器、差速器整合为紧凑单元。
氢燃料电池增程:解决纯电续航瓶颈,实现零排放。
数字孪生技术:通过虚拟仿真优化变速箱控制策略。
总结
混合动力拖拉机变速箱系统通过机电深度融合,突破了传统机械传动的效率瓶颈,是农业机械向绿色化、智能化转型的核心技术。未来,随着电池技术、智能控制算法的进步,其经济性和可靠性将进一步提升,推动可持续农业的发展。
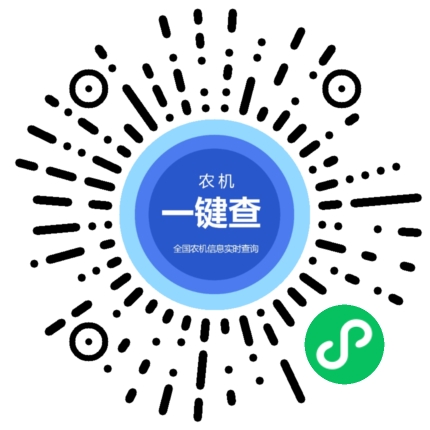
小程序扫码观看
更多农机资讯尽在农机一键查
版权声明:本文仅代表作者观点,不代表农机新闻网立场。 本文为分享行业信息所用,如需转载,请联系原作者。