现代车辆中,悬挂技术是底盘技术中重要的一环,大马力拖拉机的悬挂技术作为保证拖拉机作业过程中的操作舒适性和燃油经济性的核心技术之一,在很大程度上决定着拖拉机的高端成色。
1 技术原理与核心优势
悬挂系统作为现代拖拉机的核心技术载体,已从简单的减震功能演进为集机械、液压、电子控制于一体的智能响应系统。全球领先的拖拉机企业通过结构革新与智能控制融合,在作业稳定性、土壤保护和能源效率三大维度实现了跨越式突破。
1.1 结构革新与性能突破
独立运动解耦设计:以凯斯Quadtrac 715为代表的四履带独立悬挂系统,通过独立液压缸+蓄能器组合,使各车轮垂直运动自由度完全解耦。该系统单轮最大行程达300mm(传统设计<100mm),可吸收90%田间颠簸能量,驾驶室垂直振动加速度降低42%,大幅提升驾驶舒适性。
动态接地压力调节:约翰迪尔9RX系列搭载的ActiveSeat™系统,通过实时调节轮组接地压力,在坡地作业中减少打滑损失,牵引效率提升18%,燃油消耗降低15%。其核心在于多传感器融合控制(加速度计+位置传感器+北斗RTK),实现毫秒级地形响应。
模块化悬挂单元:CLAAS Xerion 5000采用的油气复合悬挂,将液压缸与氮气蓄能器集成于紧凑模块。蓄能器作为“液压弹簧”,通过气体压缩膨胀自适应负载变化,相比机械弹簧减震效率提升35%,维护频次降低40%。
1.2 地形适应性与土壤保护
仿地形轮廓追踪:凯斯新型悬挂的中间辊设计可完全贴合地表轮廓,即使在地面起伏达25°的恶劣工况下,仍能保持90%的额定作业速度。与刚性底盘相比,湿地作业效率提升30%。
土壤压实深度控制:德国农业研究所(DLG)测试表明,配备TERRA TRAC系统的CLAAS拖拉机,其接地比压降至0.35kg/cm²(传统轮式约1.2kg/cm²),土壤压实深度减少40%,玉米出苗率提升12%。这得益于三角履带将载荷分散于1.7倍接地面积,显著降低单点压强。
动态重心补偿:俄罗斯维亚特卡国立大学开发的物理模型,通过实时计算车辆-货物系统联合重心,结合电控悬挂调整车身姿态。在横向坡度15°的工况下,侧翻风险降低50%,轮胎滑移率控制在8%以内。
2 全球领先技术方案解析
当前国际高端拖拉机市场已形成四大悬挂技术路线,各自针对不同作业场景实现性能最优化。
表:全球主要悬挂技术方案对比
技术路线 | 代表机型 | 核心创新 | 适用场景 | 性能增益 |
电液主动悬挂 | 约翰迪尔9RX 640 | 多传感器PID闭环控制 | 大型平原农场 | 燃油效率↑15% |
被动油气悬挂 | CLAAS Xerion 5000 | 氮气蓄能器+低摩擦油缸 | 中等起伏地形 | 维护成本↓40% |
履带复合悬挂 | 凯斯Quadtrac 715 | 三角履带+独立电液单元 | 湿地/坡地 | 牵引效率↑18% |
智能联动悬挂 | CLAAS CEMOS | 多维后悬挂机构+ISOBUS集成 | 精准农业 | 耕作油耗↓14% |
2.1 电液主动悬挂系统
多区段协同控制:约翰迪尔ActiveSeat™系统通过16点压力传感器网络,以50ms响应速度动态调节液压缸压力。其控制算法基于40年田间数据库训练,可预测土壤阻力变化并预调整姿态,使坡地作业车身俯仰角波动控制在1°内(国产PID系统>5°)。
成本效益平衡:尽管系统单价增加$2.8万,但通过燃油节省(年$9万)与效率提升(20%作业面积覆盖)可在2年内收回投资。黑龙江农垦数据显示,该机型在1万亩规模农场的年综合效益达¥27万。
2.2 履带复合悬挂系统
凯斯Quadtrac 715的创新在于双技术融合:
三角履带分散压力:驱动轮直径增大11%,橡胶履带宽度扩展5%,接地面积达传统轮式的2.3倍,湿地通过性提升显著。
独立悬挂单元适应地形:惰轮与中间滚轮独立液压控制,配合自动轨道张力系统,实时优化履带接地形态。该系统润滑点减少60%,实现免维护衬套设计,故障间隔提升至2000小时。
2.3 智能联动悬挂系统
CLAAS荣获Agritechnica创新银奖的多维悬挂控制系统,代表了悬挂技术与农具协同的巅峰:
液压上拉杆集成传感:通过机具侧传感器与ISOBUS协议,系统可动态调整整地机配重分布。例如将整地机重量转移至拖拉机后轴,提升牵引力利用率。
水平姿态闭环控制:施肥机作业中实时保持撒布盘水平,肥料分布均匀度提升30%,同时降低因地形倾斜造成的浪费。
3 技术挑战与产业瓶颈
尽管顶级悬挂技术性能卓越,其产业化仍面临可靠性、成本及控制算法等多重瓶颈。
3.1 可靠性困境
液压系统耐污缺陷:田间粉尘导致比例阀卡滞问题突出。国产系统因油液清洁度仅NAS 10级(国际ISO 4406 16/13级),阀芯卡滞故障率比进口产品高3倍,故障间隔仅800小时(国际标准2000小时),单次维修成本达$1.2万。
结构疲劳风险:重载深松作业时(阻力>8吨),悬挂臂承受交变应力。国产铸件抗弯强度不足进口特种钢(如SSAB Hardox 500)的60%,断裂风险高3倍。宝钢BFS系列特种钢虽达1600MPa强度,但成本仍高30%。
3.2 成本经济性失衡
四轮独立悬挂系统推高整机成本结构:
制造成本增幅59%:单价达$35万(传统机型$22万),主要来自高精度位移传感器(如MTS Temposonics单价超$2000)及液压模块。
使用成本倍增:液压油更换周期缩短至2000小时/次(传统4000小时),年维护成本达$1.8万,较传统机型增加100%。
3.3 控制算法短板
自适应能力不足:国产系统多采用固定参数PID控制,缺乏田间大数据训练。在黏重土壤中响应延迟超200ms,导致车身摆动幅度达进口机型2倍。
多机协同协议缺失:凯斯Quadtrac支持10台设备集群作业,而国产系统需加装转换器(成本¥8000/台)实现互通,且同步精度下降40%。
4 创新发展趋势与战略展望
面对技术挑战,全球领先企业正通过材料革新、控制升级与商业模式创新三维突破,重塑悬挂技术未来。
4.1 技术路线演进
混合架构过渡期(2025-2027):徐工专利CN115123099A推出前桥独立+后桥刚性组合,成本增幅控制在15%。其机械式扭杆弹簧方案虽行程仅150mm,但满足丘陵茶园等场景需求。
全线控底盘时代(2030+):借鉴徐工XDE240矿卡技术,轮毂电机驱动+主动悬挂融合成为趋势。电机直接控制车轮扭矩分配,取消机械传动链,响应时间缩短至20ms。
4.2 核心技术突破点
耐污液压元件:江苏悦达流量共享系统(专利CN120175697A)通过比例分配变量泵,实现多执行器协同。配合歌尔股份IP69K级耐尘传感器,将阀芯卡滞故障率降低70%。
强化学习算法:江苏大学开发的地形预瞄模型,通过北斗RTK(精度±2cm)+毫米波雷达构建数字高程模型(DEM),在黑河测试中减少车身摆动42%。
4.3 产业生态构建策略
政策驱动:借鉴甘肃CVT补贴政策,对独立悬挂机型追加10%购置补贴。建立东北黑土、西北黄土等典型土壤万小时测试数据库。
跨产业联盟:组建“悬挂系统创新联合体”(主机厂+液压企业+高校),攻关密封件/传感器卡脖子环节。例如SKF耐高压旋转密封件寿命达8000小时,国产仅3000小时。
表:悬挂技术发展路线与产业协同重点
阶段 | 技术目标 | 成本控制 | 政策支持 | 产业链分工 |
近期(2025-2027) | 故障间隔≥1500小时 | 压缩至国际水平80% | 追加10%购置补贴 | 特种钢本土化(宝钢) |
中期(2028-2030) | 响应时间≤80ms | 模块化设计降本30% | 碳积分奖励制度 | 传感器国产化(歌尔) |
远期(2030+) | 全线控底盘集成 | 全生命周期成本低于传统 | 主导ISO 20000标准 | 开源控制协议联盟 |
5 结论:技术重构农业生态
拖拉机悬挂技术的进化,本质是土壤保护经济学与人机协同工程学的深度耦合。从凯斯Quadtrac的履带接地优化到CLAAS CEMOS的智能联动控制,顶级技术正推动农业机械从“力量输出者”向“生态合作伙伴”转型。
未来破局需把握三大核心:
场景化技术落地:高附加值场景(设施农业/有机农场)优先推广被动悬挂方案,通过土壤保护收益覆盖成本增量。例如葡萄园管理机械损伤降低30%,每亩增收¥17015。
数据驱动控制进化:建立国家级农田作业数据库,训练悬挂系统工况自适应算法。约翰迪尔凭借4000万小时田间数据,使控制策略超前预测300ms地形变化。
循环经济模式创新:推广“土壤保护型农机”认证制度,对独立悬挂机型实施碳积分奖励。黑龙江农垦试点显示,减少土壤压实可使后续耕作油耗降低9%,形成全链条收益闭环。
悬挂技术的终极价值不仅是提升单机性能,更是通过保护土壤微生态、优化作物生长基础,构建可持续农业的底层支撑。随着2025年凯斯全悬架底盘技术量产,以及CLAAS 3A集团(CLAAS-AgXeed-Amazone)推动的开放协议生态,悬挂系统将从“昂贵选配”进化为“智能农业核心基础设施”,最终实现土地生产力与机械效率的和谐统一。
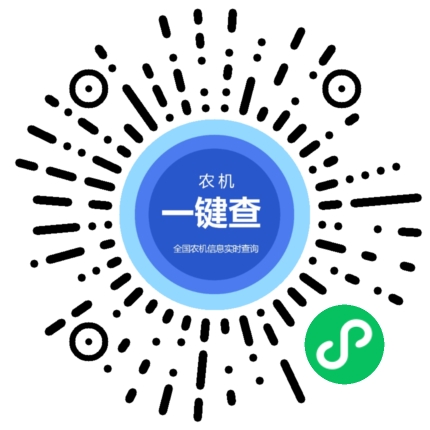
小程序扫码观看
更多农机资讯尽在农机一键查
版权声明:本文仅代表作者观点,不代表农机新闻网立场。 本文为分享行业信息所用,如需转载,请联系原作者。